فرآیند تولید مستربچ
فرآیند تولید مستربچ شامل چهار مرحله فرمولاسیون، خوراکدهی، اختلاط و الککردن است:
۱-فرمولاسیون
اولین و مهمترین مرحله، فرمولبندی رنگ و میزان افزودنی است. در این مرحله توزین دقیق تمام اجزاء فرمولاسیون انجام میگیرد که در بعضی موارد لازم است که این ترکیبات با سرعت بالا ترکیب شوند تا نتیجه بهتری ارائه دهند
۲-خوراکدهی
میزان تغذیه اجزاء متناسب با خروجی دستگاه تنظیم میشود.
۳-اختلاط
اختلاط مذاب در دمای مخزن تنظیم میشود تا مخلوط ذوب شود. دمای نامناسب باعث اختلال در برش گرانول و پخش پودر میشود.
اختلاط شامل ۴ مرحله زیر است:
-
- فرآیند خیسشوندگی پیگمنت، افزودنی و پرکننده
- اختلاط فیزیکی: اختلاط و پخش پیگمنت و افزودنی در پلیمر پایه
- توزیع: توزیع پیگمنت، افزودنی و پرکننده در مذاب پلیمری
- پراکندهسازی پایدار کردن این مخلوط و جلوگیری از کلوخهشدن
مهمترین مرحله تولید مستربچ، اختلاط است و متداولترین روش پخش مناسب افزودنی یا رنگ از طریق ترکیب اجزاء به صورت مذاب حاصل میشود.
مرحله اختلاط با بهرهگیری از دستگاههای زیر انجام میشود:
-
- مخلوطکنهای داخلی همانند بنبوری: بهترین انتخاب برای تولید مقدار زیادی از این افزودنیها
- مخلوطکنهای داخلی مداوم
- اکسترودر دو مارپیچ
- ماشینهای تک مارپیچ
- مخلوطکنهای سرعت بالا به همراه اکسترودر تک مارپیچ
مهمترین دستگاه مورد استفاده در فرآیند اختلاط و تولید مستربچ که به طور گسترده در صنعت ایران به کار میرود،اکسترودر است. در این روش پلیمر و افزودنیها درون دستگاه اکسترودر ذوب و با هم ترکیب شده و سپس از انتهای اکستروژن خارج میشوند. در این روش خط تولید مستربچ به طور مختصر عبارت است از سیستم تخلیه، سیستم خوراکدهی، اکسترودر، سیستم خنک کننده، سسیستم برش، انبارش و بستهبندی.
اکسترودر دو پیچه همسو گرد: این فرایند شامل وزن کردن، وارد کردن خوراک، انتقال، ذوب کردن، پخش کردن و همگن کردن، خارج کردن گازهای مزاحم، فیلتر کردن و گرانول کردن است.
کلید بنیادی درک و بهینه سازی فرآیند اختلاط در تشخیص تمایز، مکانیسم های آن شامل پراکندگی و توزیع است. مکانیسم پراکندگی شامل کاهش اندازۀ اجزاء چسبندۀ کوچک در یک سیستم چند فازی است. مکانیسم توزیع، فرآیند پخش ذرات کوچک در سراسر ماتریس به منظور دست یابی به پخش فضایی خوب است.
در هر دستگاه اختلاط، این دو مکانیسم به صورت هم زمان یا مرحله به مرحله انجام می گردد. پراکنش تحت تاثیر موازنۀ دو عامل نیروهای چسبندگی ایجاد کلوخه و نیروهای هیدرودینامیک تخریب است. همچنین، بزرگی تنش های اعمالی، نقش تعیین کننده ای در توزیع اندازۀ قطرات دارد.
پراکندگی و توزیع پیگمنتها در مستربچ های پلی اتیلن، اختلاط موثر به کمک ترکیبات سازگارکننده، سازگارکنندهها با عنوان علمی ترکیبات آمفی فیلیک، دارای یک سر آب دوست و یک سر آلی دوست هستند و به دلیل ماهیت شیمیایی خاصشان، باعث افزایش پایداری حرارتی، سازگارسازی پلی اولفینها و پلیمرهای مهندسی، تشکیل لایۀ پایدار بر روی سطح افزودنی، پیگمنت یا پرکننده از طریق کنش متقابل با آنها و ایجاد اتصال آنها به ماتریس پلیمری میشوند.
۴-الککردن
مستربچ نهایی باید به اندازهای محکم و با سایز مناسب باشد که مصرف کننده نهایی بتواند در مرحله تولید خود با مشکل خوراک دهی روبرو نشود. بنابراین لازم است تا از الک هایی برای اطمینان از مناسب بودن اندازه گرانول مستربچ استفاده شود.
بهینه سازی خطوط کامپاند و مستربچ
در صنایع از قبیل تجهیزات تزریق پلاستیک و یا اکسترودها نمی توان مستربچ را به پایههای پلیمری اصلی اضافه کرد. در چنین شرایطی کارخانجات ناچار به استفاده از کامپاند میشوند تا به این ترتیب کیفیت محصول نهایی آنها کاهش پیدا نکند. از طرفی از لحاظ اقتصادی و بهداشتی استفاده از کامپاند برای تولید محصول نهایی بسیار به صرفهتر از مستربچ است. چرا که از هزینه ناشی از تمیزکاری و ترکیب مستربچ و پایه پلیمری را حذف خواهد کرد.
برای تولید کامپاند باید فرآیندهای مختلفی طی شود. اصلیترین فرآیندی که در تولید کامپاند و مستربچ باید مورد توجه قرار بگیرد، فرآیند ذوب شدن است. در فرآیند ذوبشدن مواد افزودنی و پلیمرهای پایه، با نسبت معینی با یکدیگر ترکیب میشوند. ترکیب این مواد در دستگاهی به نام اکسترودر انجام میشود. توزیع مناسب افزودنیها در پلیمر پایه اهمیت بسیا زیادی در افزایش کیفیت محصول نهایی دارد.
در ادامه باید ترکیب حاصل خنک شود تا بتوان برای تولید محصول نهایی اقدام نمود. برای این منظور ترکیب مورد نظر را به دستگاه دیگری منتقل میکنند که اصطلاحا به نام خنک کننده شناخته میشود. پس از سرد شدنه مواد مورد نظر، حالت جامد به خود میگیرد و پس از آن به کمک دستگاههای خردکن به ابعاد کوچکی در میآیند و برای استفاده در تولید محصولات پلیمری مختلف روانه بازار میشوند
یکی از مهمترین نکات این است که پارامترهای مهمی در شیوه تولید کامپاند اثر گذارند. بهمنظور بررسی پارامترهای تأثیرگذار بر روی ظرفیت خط تولید کامپاند، میتوان به موارد زیر اشاره کرد:
قطر ماردون
یکی از تجهیزات بسیار مهم برای تولید کامپاند، ماردون است و در راستای بررسی شیوه تولید کامپاند باید به این نکته توجه داشته باشید که قطر ماردون میتواند تأثیر بسیار زیادی بر روی تولید کامپاند داشته باشد. قطر ماردونها متناسب با قدرت موتور و گیربکس تعیین میشوند. هر چه این قدرت موتور و گیربکسها بالاتر باشد، عملکرد ماردون بهتر بوده و همین موضوع باعث میشود تا ظرفیت تولید کامپاند افزایش پیدا کند.
تاثیر سرعت گردش ماردون در شیوه تولید کامپاند
نحوه تولید کامپاند به شکلی است که سرعت چرخش ماردونها تأثیر بسیار زیادی بر روی آن دارد. به همین دلیل است که هر چه سرعت گردش ماردون و گشتاور گیربکس بالاتر باشد، این مسئله منجر به خروجی بیشتر و اختلاط بهتر مواد خواهد شد. نتیجه نهایی این اتفاق نیز سرعت بالا و تولید حجم بیشتری از کامپاند است.
تاثیر پلیمر و مواد افزودنی بر شیوه تولید کامپاند
همانطوری که اشاره کردیم، برای ساخت کامپاندها لازم است تا از انواع مختلفی پلیمر و مواد افزودنی استفاده شود. نوع پلیمرهای مورد استفاده و همچنین درصد مواد افزونی از مهمترین عواملی هستند که بر روی میزان خروجی کامپاند تأثیر گذاشته و کیفیت تولید کامپاند را تحت شعاع قرار میدهند.
بهعنوان مثال اگر از پلیمرهایی با جرم مولکولی بیشتر و یا با داشتن مواد افزودنی بیشتر و خالصتر استفاده شود، نسبت به پلیمرهایی با جرم مولکولی کمتر و یا درصد کمتر مواد افزودنی، شاهد خروجی کمتری هستیم. حتی اگر بهمنظور تولید این دسته از محصولات از ماشینآلات و سیستمهای یکسانی استفاده شود. این مسئله نشاندهنده آن است که برای بررسی شیوه تولید کامپاند باید توجه بسیار زیادی به نوع پلیمر و درصد مواد افزودنی مورد استفاده داشته باشید.
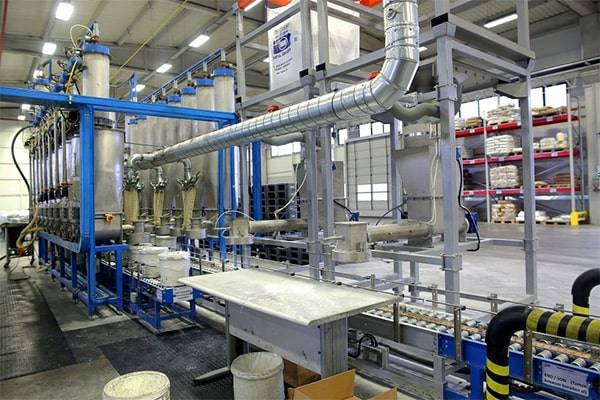